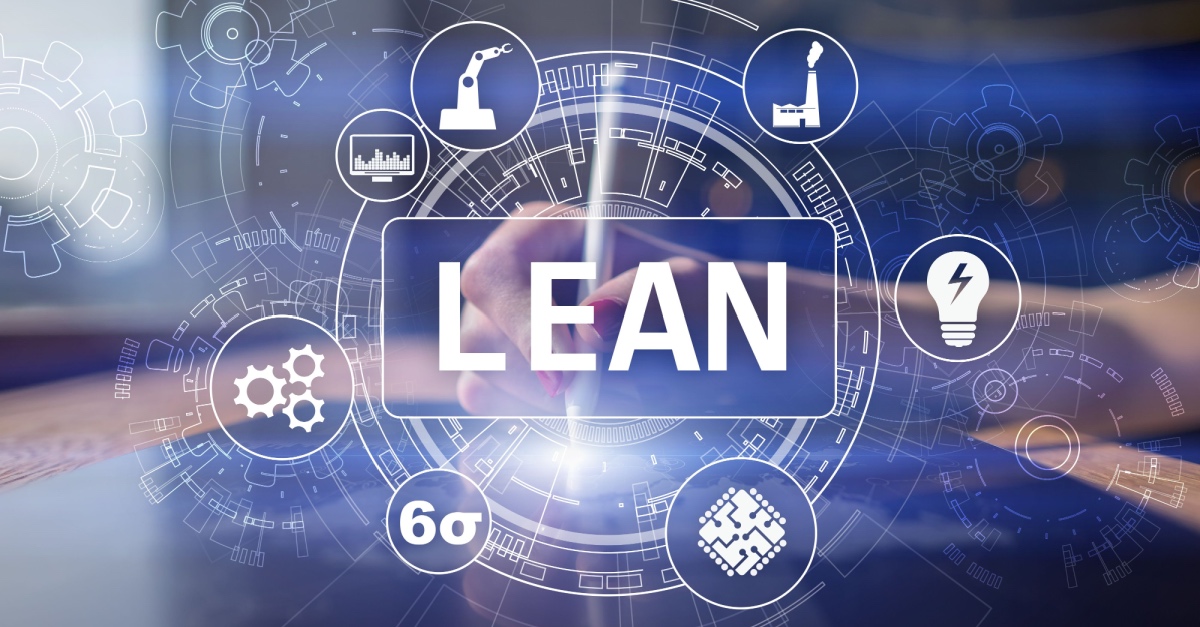
Supply Chain Now Guide to Lean Manufacturing: Tried, True, and Transformative

Lean manufacturing is all about reducing waste and increasing efficiency. Manufacturers have been implementing lean practices for decades and have stood the test of time. Now, with technological advancements, lean methodologies can be more transformative than ever before.
“Integrating automation into lean manufacturing is a powerful strategy. Unlike traditional automation, which often aims to increase production capacity without considering real needs, lean automation focuses on the smart and selective application of technologies to meet specific continuous improvement goals and eliminate inefficiencies,” the Kaizen Institute said.
“Digital transformation provides an unprecedented opportunity for implementing lean,” it continued. “When applied within lean, tools like the Internet of Things (IoT), artificial intelligence (AI), and data analytics can revolutionize how organizations detect and eliminate waste.”
What is Lean Manufacturing?
In “The Machine That Changed The World,” published in 1990, lean production is hailed as “Toyota’s secret weapon in the global car wars.”
The Toyota Production System was developed following World War II from “a series of simple innovations … to provide both continuity in process flow and a wide variety in product offerings,” according to the Lean Enterprise Institute.
In “Lean Thinking,” a 1996 follow-up to “The Machine That Changed The World,” authors James Womack and Daniel Jones introduced a five-step process to guide managers through a lean transformation.
- Specify value from the standpoint of the end customer by product family.
- Identify all steps in the value stream for each product family, eliminating steps that do not create value.
- Make the value-creating steps occur in a tight sequence so the product will flow smoothly toward the customer.
- As flow is introduced, let customers pull value from the next upstream activity.
- As value is specified, value streams are identified, wasted steps are eliminated, and flow and pull are introduced. Repeat this process until a state of perfection is reached.
In 2007, Womack and Jones simplified the process to the three focus areas we are more familiar with today: purpose, process, and people.
Purpose: “The primary purpose of any organization and first step in any lean thought process is to correctly specify the value that the customer seeks in order to cost-effectively solve the customer’s problems so the organization can prosper,” the Lean Enterprise Institute said.
Process: The ideal process – the value stream – to achieve the objective is valuable, capable, available, adequate, and flexible.
People: Someone must be responsible for each value stream. There also must be a master plan, frequent improvement cycles, and standard work management for every step in each process.
Lean Manufacturing: An Old Solution with Modern Benefits
Henry Ford is credited with first integrating an entire production process in 1913. The Lean Enterprise Institute said his flow production system was lauded as a “truly revolutionary break” from standard manufacturing practices.
More than a century later, lean manufacturing principles are still an integral component of complex modern supply chains. Shoplogix said lean management remains “a go-to for many companies” to increase efficiency.
“At its core, it’s all about producing high-quality products faster and cheaper by eliminating waste in the form of excess materials, unnecessary steps, or idle time,” Shoplogix said. “This approach involves closely monitoring production processes, identifying areas where resources are being wasted, and then taking swift action to address these issues. It’s not just a one-time fix but a continuous cycle of examining, improving, and streamlining operations.”
Increased Efficiency
Lean practices streamline processes and reduce cycle times. In addition to Toyota and Ford, companies that have improved their efficiency with lean practices are Amazon, Caterpillar, John Deere, and Nike.
Cost Savings
“Unnecessary expenses are detrimental to any organization, but in supply chain, these expenses are inevitably passed on to the end user,” the Association for Supply Chain Management (ASCM) said, explaining that implementing lean practices can “improve value by reducing the amount spent on unnecessary steps during manufacturing and fulfillment processes.”
Improved Quality
“The significance of lean manufacturing transcends mere cost reduction or operational efficiency,” the Kaizen Institute said. “It aims to foster a continuous improvement culture, where active participation of employees at all levels of the organization is crucial. This approach enhances the quality of products and processes and contributes to a better work environment.”
Three Key Lean Manufacturing Techniques
Lean manufacturing has evolved with technological advancements, but three tried-and-true practices remain fundamental.
Value Stream Mapping
Mapping the value stream entails identifying each step from product conception to delivery and determining how value is created at each stage. The goal is to determine which steps add value and which do not, laying the groundwork for waste elimination.
“Value stream mapping typically begins with a team creating a current state map by capturing the actual condition of a value stream’s material and information flow,” the Lean Enterprise Institute said. “Subsequently, the team draws a future state map, a target image of how the material and information should flow through the value stream. Repeatedly doing the value stream mapping process is the simplest and best way to teach yourself and your colleagues how to see value-adding versus nonvalue-adding process elements.”
5S Methodology
Lean Production said 5S is the “widely heralded method for efficiently organizing manufacturing workplaces.” The 5S activities are to sort, straighten, shine, standardize, and sustain.
The 5S methodology was developed as part of the Toyota Production System, according to Lean Production, because the automaker “sought to radically eliminate any part of the automotive production process that contributed to muda, the Japanese word for waste.”
Just-in-Time (JIT) Production
Toyota also is credited with developing the just-in-time (JIT) strategy to increase efficiency and decrease waste by receiving raw materials only as they are needed for the production process.
“Toyota understood that the ability to maintain a consistent flow of manufacturing lessened the waste generated by stopping and then starting up again. As a result, the company created the just-in-time (JIT) system and perfected its ability to produce automobiles on a consistent basis. This enabled harmony through all aspects of the manufacturing process, from receiving customer orders to producing vehicles efficiently to delivering finished vehicles quickly,” ASCM said.
The Future of Lean Manufacturing
Today’s manufacturing workers also are empowered by data, digital tools, and advanced analytics, the Boston Consulting Group (BCG) said. “Operators employ data-driven technologies to evaluate productivity losses in detail, optimize corrective measures, and seamlessly communicate across teams. At the same time, they leverage AI’s predictive and prescriptive capabilities to improve safety, quality, and reliability. These enhancements reduce waste, promote productivity gains, and support the sustainment of lean practices.”
Still, only 16% of companies surveyed by BCG Global of about 1,800 manufacturing executives earlier this year said they had achieved their AI-related goals.
“Nearly all companies said they face challenges in scaling their AI solutions,” BCG said. “To realize value from digital and AI integration at scale, companies will need to focus sharply on people and processes – even more than they do on technology and algorithms.
“Manufacturers need to define their vision, build capabilities, and orchestrate the activities of multiple stakeholders. They must support these efforts within the right data infrastructure and governance, as well as establish the prerequisites for scaling technology across the production network.”
The benefits of lean manufacturing “extend well beyond present day,” Supply & Demand Chain Executive said. “As new technologies, such as artificial intelligence and machine learning (AL/ML), continue to shape our society, modern businesses will be able to push the boundaries of their specialties using these practices.”
Supply Chain Now Is Your Guide to Lean Manufacturing
Supply Chain Now is the authoritative source for all things supply chain, including lean manufacturing. From podcasts to livestreams, vlogs, virtual events, and articles, Supply Chain Now delivers everything you need to know about the latest industry developments around the world.
Our supply chain podcast programming includes:
- Supply Chain Now, featuring the best and brightest in the business.
- Logistics With Purpose, a show dedicated to creating a positive impact and addressing such important issues as disaster relief, fighting hunger, and sustainability efforts.
- Digital Transformers with Kevin L. Jackson, recognized as a top 50 global digital transformation thought leader.
Our library is packed with supply chain podcasts addressing a huge variety of industry-related topics. Manufacturing-related programs include:
- “How Do Supply Chains Stay Lean in a Disrupted World?”
- “Powering a New Age of Manufacturing”
- “Innovation Trends in the Manufacturing Sector”
Check out these and other industry-leading podcasts. Listen now.